By: Zach Wood
Hi everyone! My name is Zach Wood and I am currently a 3rd year Ph.D. student in the chemistry department at USC under the mentorship of Professor Megan Fieser. The Fieser Lab broadly focuses on designing molecules that can enable sustainable transformations such as the synthesis of environmentally friendly plastics (polymers) or recycling of current plastics.
Our demand for plastics has grown exponentially over the years, with it being projected that by 2050 production for food packaging will reach 318 million tons alone. Of the plastic that we produce each year, only 2% is processed through closed loop recycling. Therefore, finding solutions to decrease the accumulation of this plastic waste will be greatly beneficial to improving the health of our environment.
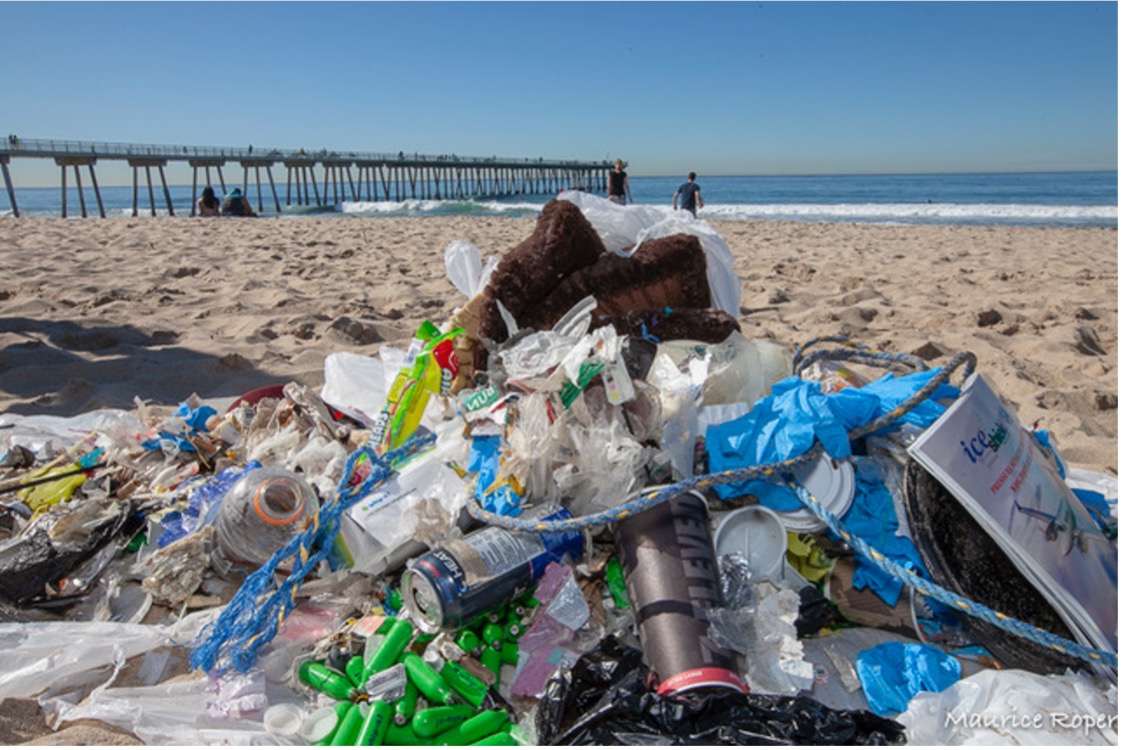
Image of plastic collected during February 2020 Hermosa Beach Cleanup. Photo taken by Maurice Roper.
The Fieser Lab is interested in utilizing rare earth metals as catalysts to synthesize sustainable polymers. The role of these catalysts is to help increase the rate at which the polymers grow while also making sure the reaction is controlled. The way I like to think about this is how coffee can act as a catalyst for my productivity: it can help me get things done faster (increased rate) while also allowing me to focus on the task at hand (control).
My summer research as a Wrigley Institute Sonosky Fellow involved synthesizing polymers that can potentially be a biodegradable alternative to plastics such as the PET used for plastic bottles. Many projects in the Fieser Lab involve synthesizing a supporting framework for the rare earth metals that adds stability to the catalyst in addition to increased control of the polymerization. However, my project focuses on using rare earth salts as catalysts, which is different than other projects in the lab because I don’t have to perform any synthesis to get to the active catalyst. This work has many potential advantages over current systems such as simplicity and cost. While my work is still being performed on a small scale in the lab, the future applications are promising and the Fieser lab is excited to pursue more research involving these rare earth salts.

Before crashing out polymers from solution that I synthesize, I document what color the reactions are after completion.
My day-to-day activities in the lab included many different experiments that ranged from setting up 20 reactions that run at the same time to analyzing the polymers that I made through methods available here at USC and the Fieser Lab. One of the most fun things that I found in the lab was the surprising feel of the plastics once I made them. Depending on the building blocks I used to make the polymer the feel could range from a viscous gel to brittle solid. Being able to feel the product you make in a chemistry lab and see how it could be used for different applications is something I have never experienced before and helps me see how my work can be directly impactful.
As I finish my summer experiments, I have reflected on how much I have enjoyed my experience in the Fieser Lab this summer. I am surrounded by awesome teammates that are supportive of my work and challenge me scientifically. Additionally, the Fieser Lab performs beach cleanups that involve not only cleaning our beaches but learning about how everyone can help solve the plastic pollution problem we currently face. Opportunities like this only help me motivate my work in the lab even more.
And finally, a big thank you to the Wrigley Institute for all their support this summer!